3D Printed Housing In NC
America has a housing shortage. Our team and affiliates, armed with 3D printing technology, plan to eliminate that shortage. TNT Development’s legacy builders can help you design the house of your dreams at an affordable price in a fraction of the time.
Odell Village Project
Odell Village is a groundbreaking 3D printed housing development project in Littleton, North Carolina designed to transform the real estate industry. This development will consist of 100 homes that are constructed using 3D Concrete Printing (3DCP) technology.
Watch the video below to learn more about this 3DCP initiative.
Odell Village: 3 Phase Plan

Learn More About Each Phase
Phase One
Phase I will feature 20 thoughtfully designed micro-units, forming a cozy and innovative bungalow village that combines modern living with a sense of community. Each micro-unit is carefully planned to maximize functionality and comfort within a compact footprint, offering high-quality finishes, efficient layouts, and smart storage solutions.
Phase I sets the foundation for a forward-thinking residential experience.
Phase Two
Phase II will introduce 64 single-family units, thoughtfully designed to provide families with comfortable, modern, and affordable living spaces. Each home will feature carefully planned layouts that prioritize functionality and adaptability, catering to the diverse needs of today’s families. With energy-efficient systems, eco-friendly materials, and high-quality craftsmanship, these homes not only offer exceptional comfort but also promote long-term sustainability and cost savings for residents.
Phase II represents a commitment to creating accessible, well-designed homes that blend affordability with the convenience and charm of a vibrant residential community.
Phase Three
Phase III will focus on ensuring the long-term success and satisfaction of the community through ongoing support, regular inspections, and community feedback initiatives. This phase emphasizes the importance of maintaining the quality, safety, and functionality of the homes while fostering a thriving and connected neighborhood. Periodic inspections will help identify and address any maintenance needs, ensuring the homes remain in excellent condition for years to come. Additionally, community surveys will provide residents with a platform to share their experiences, suggest improvements, and voice their needs, enabling us to make informed decisions about ongoing 3D printed housing developments.
Phase III is a testament to our commitment to not only increasing access to affordable housing, but cultivating a sustainable and supportive environment where residents feel heard, valued, and proud to call this neighborhood home.
Benefits of 3D Printed Housing
The market for 3DCP is growing rapidly because of increasing demand for affordable, sustainable, and quickly constructed homes. Leveraging this technology allows construction companies to tackle housing shortages by decreasing construction time, materials usage, and labor costs. The need and potential for automation in the construction industry and the impact of 3DCP on construction costs are substantial and well-documented.
- Cost Efficiency: 3DCP can substantially reduce labor costs and material waste. Its precision ensures that only the necessary material is used, leading to significant savings.
- Speed of Construction: 3DCP can build homes much faster. While traditional construction can take months or even years, 3DCP homes can be completed in weeks or even days.
- Design Flexibility: 3DCP allows for intricate and customized designs that are often difficult or impossible to achieve with traditional methods. This flexibility enables unique architectural features and personalized layouts.
- Durability and Strength: 3DCP’s layering process creates robust structures that can withstand stresses better than traditional construction, making them more durable and long-lasting.
- Sustainability: 3DCP’s precision minimizes construction waste, making it a more sustainable option.
- Energy Efficiency: 3DCP homes can be designed with superior insulation, improving their thermal properties and lowering energy consumption.
- Rapid Response to Housing Needs: 3DCP can quickly provide housing in response to natural disasters or housing shortages, offering immediate shelter and addressing urgent needs.
Other 3D Concrete Printing Products

Furniture & Decor
This market segment is growing rapidly because of rising interest in custom, durable, and sustainable designs. The range of 3DCP applications includes indoor and outdoor uses with innovations such as modular furniture, facade elements, and decorative pieces that are highly customizable and more eco-friendly than traditional manufacturing. Manufacturers use 3DCP to create intricate designs that are difficult or cost-prohibitive to achieve with standard concrete casting methods.
•Customization: 3DCP allowsfor highly customized designs, enabling unique and intricate furniture pieces that can be tailored to individual preferences and needs.
• Sustainability: This method can use recycled materials and produce less waste than traditional manufacturing processes, making it more environmentally friendly.
• Cost Efficiencies: 3DCP can be a more cost-effective way to produce furniture by reducing material waste and labor costs.
• Speed: The design to finished product process is much faster than traditional manufacturing.
• Complex Designs: 3DCP can easily create complex geometries that would be difficult or impossible to achieve with traditional manufacturing methods.
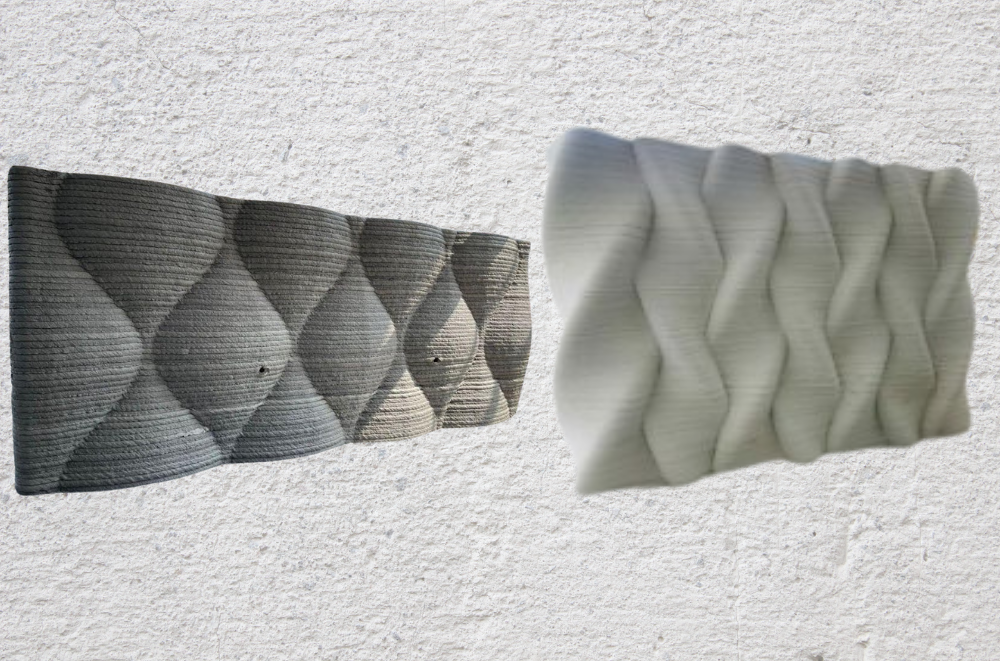
Retaining Walls
Retaining walls are essential structures designed to provide stability and support in areas where soil needs to be retained at different levels. They are commonly used in both residential and commercial projects to prevent erosion, manage water flow, and create usable spaces on sloped or uneven terrain. Whether for decorative garden borders or large-scale construction, retaining walls play a critical role in shaping and protecting the built environment.
•Durability: Can be made from solid, durable materials providing excellentstructural integrity.
•Efficiency: 3DCP’s precision reduces material waste and ensures that the walls are built to exact specifications, improving overall efficiency.
• Cost Savings: Like furniture, 3D-printed retaining walls can reduce labor and material costs.
• Speed of Construction: Faster than traditional methods, allowing for quicker completion.
• Design Flexibility: Allows for innovative and flexible designs ideal for variouslandscapes.
Support for 3D Concrete Printing (3DCP)
3DCP and Eco-Materials are generating significant industry and market buzz because of their appeal for sustainable growth. These technologies enable faster, waste-reducing construction and complex, eco-friendly designs that align with affordable housing goals. Their potential to transform infrastructure and reduce environmental impact has sparked broad interest, making them highly marketable and sought-after in today’s environmentally conscious landscape.
TNT’s marketing efforts will focus on fulfilling its current and future contractual obligations to build 3D-printed homes. These homes are designed to address the needs of municipalities facing housing shortages and a lack of affordable housing while also providing custom attention for novice clients. Additionally, the Department of Transportation (retaining walls), Department of Defense, and military installations have shown interest in incorporating TNT’s products into various applications including 3D-printed indoor and outdoor furniture, décor, and hardscape, including in parks and recreation areas.
Our initiatives in North Carolina have gained the attention of US Senator and NC Representative, Thom Tillis. Senator Tillis has expressed via a gratitude letter, his appreciation for our team and partners’ efforts in our commitment to positively impacting the communities of North Carolina.
Support Letter From NC Senator, Thom Tillis
(Click The Letter To Expand and Read)
Access It
Making home ownership possible across all ages and demographics. Rural communities, as well as low income urban communities, are struggling to build new residential units across the America and abroad.
Build It
Using 3D technology for residential constructions, the cost to build does not equal the cost to sell throughout rural and many urban communities. We aim to change this and make 3DCP an attainable option for them.
State of The Art 3D Concrete Printer Equipment
On August 8, 2024 TNT and Tvasta completed commissioning the FIRST-EVER Tvasta MOBILE ROBOTIC ARM SYSTEM deployed in the United States – the RD20. TNT Development has invested $650,000 to acquire its 3DCP RC20 device and its product catalog. We will continue to partner with Tvasta in the development of a 3DCP facility.
Learn More Through Our 3D Printing Project Journal Playlist
Work With An Innovative Construction Company
Contact Us
TNT Developement is a subsidiary of Cross N Crowns Ventures, Inc.
(c) TNT Developement 2021